Skip to main content
Preparation Of Cost Sheet
Cost Sheet Preparation: Autocomp Ltd
1. Cost Sheet Overview
-
Definition: Final output of the costing department showing cost of production per unit.
-
Service Industry: Analogous cost sheet shows cost of delivering each service.
2. Company & Products
-
Company: Autocomp Ltd.
-
End Products:
-
Materials / Components (R‑101 to R‑105)
-
Production Facilities:
-
Machine Shops: M‑101, M‑102, M‑103
-
Assembly Shops: A‑101, A‑102
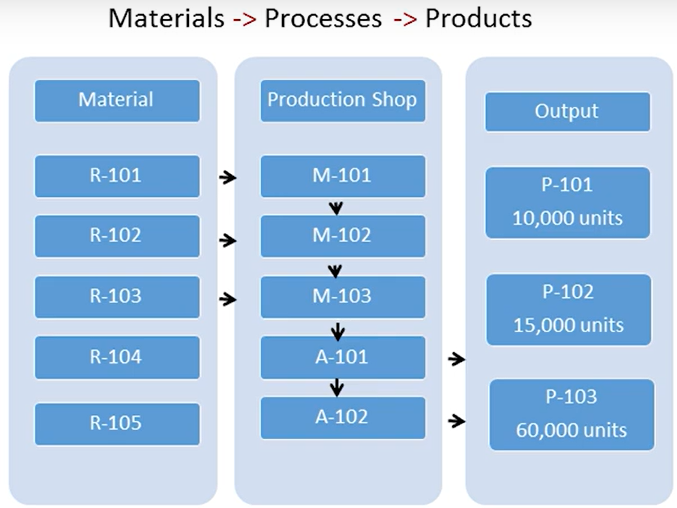
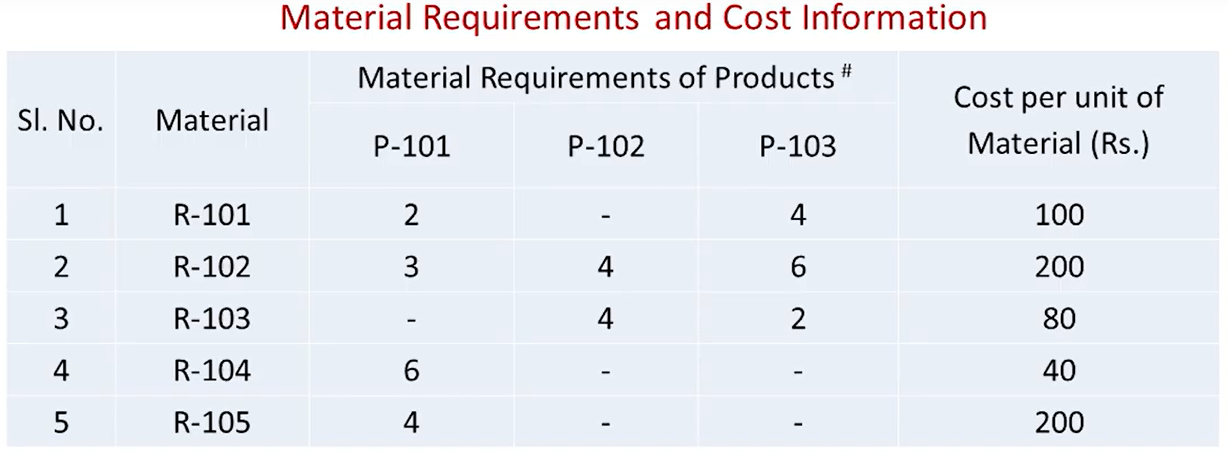
3. Material Requirements & Costs
-
Per‑unit material mix:
- P‑101 uses 4 materials
- P‑102 uses 2 materials
- P‑103 uses 3 materials
-
Compute per‑unit material cost:
- Multiply quantity of each material × cost per unit.
-
Results:
- P‑101: ₹1,840
- P‑102: ₹1,120
- P‑103: ₹1,760
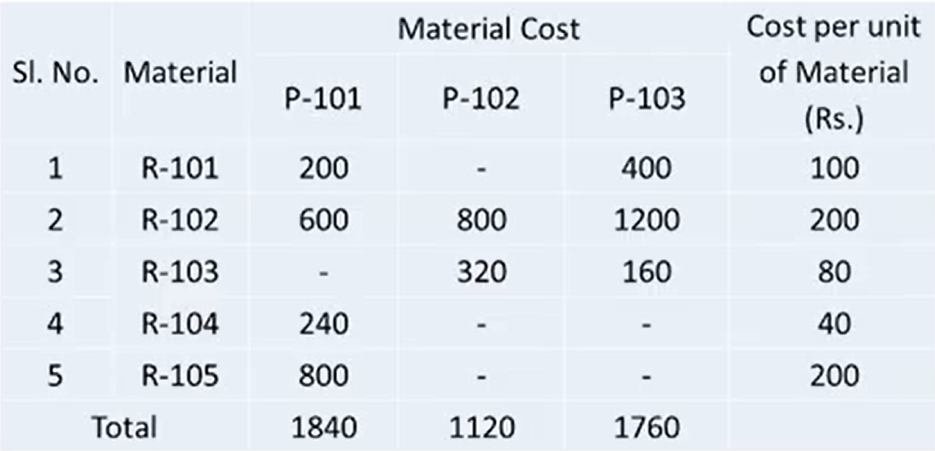
-
Monthly material cost:
- P‑101: 10,000 × ₹1,840 = ₹18.40 million
- P‑102: 15,000 × ₹1,120 = ₹16.80 million
- P‑103: 60,000 × ₹1,760 = ₹105.60 million
4. Machine & Assembly Hour Requirements
-
Throughput rates (units/hour) per machine center vary by product.
-
Compute hours required:
Hours = Units produced / Units per hour
-
Capacity vs. Usage (per month = 200 hrs):
- M‑101: 200 hrs used (full)
- M‑102: 150 hrs used (idle 50 hrs)
- M‑103: 125 hrs used (idle 75 hrs)
- A‑101: 25 hrs used (idle 175 hrs)
- A‑102: full utilization for those products that require it
5. Allocating Production Center Costs & Idle Capacity
-
Cost pools per center:
- Labor
- Power & fuel
- Depreciation
-
Idle capacity treatment options:
-
Charge full cost (including idle hours) → customer bears all expenses.
-
Charge only utilized hours → exclude idle‑time cost from product.
-
Assumption for this exercise: Option 1 (charge full cost).
6. Machine / Assembly Hour Rates
-
Rate per hour = (Total center cost) ÷ (Actual hours worked)
-
Example (M‑101):
- Total cost ₹2,450,000 ÷ 200 hrs = ₹12,250/hr
-
Note: Higher rates result from low utilization (idle time).
7. Assigning Production Center Cost to Products
8. Labor Cost Allocation (for support of common‑cost allocation)
-
Compute labor rate per center:
- Center labor cost ÷ hours worked
- E.g., M‑101: ₹300,000 ÷ 200 hrs = ₹1,500/hr
-
Product‑wise labor cost:
- Multiply product labor hours × labor rate
- E.g., P‑101 labor = 1,087 hrs × ₹1,500 = ₹1.63 million
-
Results:
- P‑101: ₹1.63 million
- P‑102: ₹0.97 million
- P‑103: ₹0.45 million
9. Support Department Cost Allocation
-
Departments: Purchase, Stores, Quality Control, Maintenance, Accounting & Admin, Canteen
-
Allocation bases:
Department |
Allocation Base |
Purchase |
Material cost |
Stores |
Material cost |
Maintenance |
Machine hours |
Quality Control |
Units produced |
Canteen & Personnel |
Product labor cost |
Accounting & Admin |
Units produced |
-
Process:
- Compute each department’s total cost share per product using its chosen base ratio.
10. Final Cost Sheet & Unit Costs
-
Cost categories:
- Material
- Production center (machine + assembly)
- Support center (all service departments)
-
Per‑unit costs:
Product |
Total Cost/Unit (₹) |
P‑101 |
3,009 |
P‑102 |
1,782 |
P‑103 |
1,886 |
-
Cost structure (% of unit cost):
- Material cost: largest share
- Production center cost: next largest
- Support center cost: relatively small
- P‑103 is highly material‑intensive (≈ 93 % material).
No Comments